- Home
- Mechanical Repair
- Weld Guns
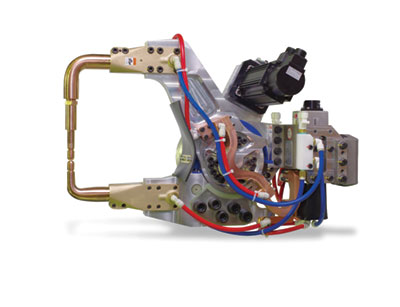
Weld Gun Repair Service
Welder guns are essential components in welding and manufacturing operations, and ensuring their proper functioning is crucial for maintaining productivity and achieving high-quality welds. In addition to keeping your weld guns operating at peak performance levels, Perfection Servo's repair service maximizes the lifespan of these tools and minimizes future repair needs.
Common Weld Gun Repair Needs
Over time, normal wear and tear can lead to decreased performance and potential breakdowns in weld guns, impacting production schedules and overall efficiency. Our innovative and comprehensive rebuild and repair program for resistance weld guns, arms, tip holders, cylinders, and more can significantly reduce your expenses by extending the lifespan of your tools.
Weld Gun Repair Process
Perfection Servo is focused on providing high-quality repair services, effective solutions, and rapid turnaround times, consistently pushing for process enhancements.
Each repair is backed by a 12-month operational warranty and complies with ISO 9001:2015 standards.
Quality Assurance
At Perfection Servo, we customize our repair processes to meet the specific needs of your production operations by continually advancing our testing facilities to keep up with the latest industry standards. Our extensive industrial and automation repair testing includes a 12-month warranty and a detailed test report that tracks each unit’s performance during evaluations.
Our advanced testing includes detailed reports for every repair, explaining both the procedures and results. Transparent and precise quotes are provided following evaluations, detailing the necessary refurbishments required to elevate each unit to or above OEM standards. These reports are critical for maintenance teams to determine the causes of malfunctions.
Credentials
Our Certified Repairs feature:
Expertly Trained and Certified Technicians – Our technicians are continuously updated with the latest in component repair and testing operations, holding certifications from OEMs, the International Fluid Power Society, and the Electronics Technicians Association.
Rigorous System Testing – Each repair undergoes comprehensive testing to ensure it meets or exceeds OEM specifications. Our tests are performed in conditions that mimic real-world plant operations, ensuring the dependability of our repairs.
Premium Replacement Parts – We use only new, OEM, or equivalent parts in all our repairs. For unique or discontinued components, our engineers meticulously develop appropriate replacements.
Extensive Documentation – We thoroughly record each step of the repair process, from equipment manuals to specific repair actions. Each repair includes a detailed report that outlines the procedures performed and the testing conducted.
Repair Process
- Receiving: Upon their arrival, parts are unpacked, cataloged, and photographed. We collect all necessary technical, order-related, and customer information to ensure a well-informed repair process. Each part is tagged with a tracking barcode for efficient monitoring.
- Evaluation: Parts are directed to the relevant department for thorough evaluation.
- Quoting: After the evaluation, our Inside Sales team creates a detailed repair quote for your approval, which outlines the required restorations to bring the unit up to OEM standards and any issues identified.
- Approval: Once approved, the repair is assigned to the technician who is best suited for that specific part.
- Repair: The part is treated according to designated repair and testing protocols. Our technicians replace any failing or potentially problematic components and then conduct an extensive testing phase.
- System/Quality Test: Following the testing phase, a Senior Technician evaluates the part’s functionality within our testing system and verifies the accuracy of the Repair and Test Report.
- Test Reports: Each repaired unit comes with a Test Report detailing its performance in the final testing. Most repairs also include an installation checklist, and our technicians are on hand to help with installation and troubleshooting.
- Shipping: After completion, our automated system alerts the shipping department of any special customer shipping instructions. Repairs are carefully packaged to ensure they arrive in excellent condition.