- Home
- Electronic Repair
- PCB's
Industrial PCB Repair
Perfection Servo specializes in PCB repair and remanufacturing services for industrial clients. With our quick turnaround, competitive pricing, and advanced PCB testing and repair fixtures, we get your systems back online with minimal downtime and investment. Our quick turnaround times and competitive pricing make us a go-to choice for PCB refurbishment and repairs nationwide.
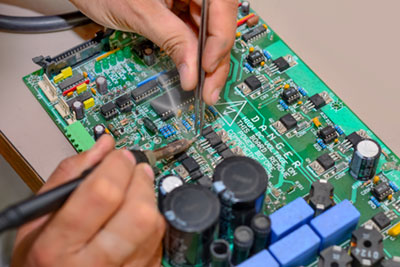
Signs of Failing PCBs
Since they mostly operate inside your equipment and behind the scenes, it can be difficult to determine if your PCB has an issue. Signs that you may be having PCB issues include:
- Erratic Behavior: Unexplained glitches, intermittent operation, or random shutdowns in the machinery controlled by the PCB could indicate an issue with the board itself.
- Electrical interference or disruptions with other equipment
- Unusual sounds or smells (especially burning or ozone smell)
When inspecting PCBs themselves, look for the following:
- Physical Damage: Visible cracks, burns, or charred components on the PCB.
- Overheating: Parts of the PCB or specific components getting excessively hot during operation.
- Corrosion or Moisture Damage: Signs of rust, corrosion, or moisture on the PCB, which can lead to short circuits or component failure.
PCB Repair Process
Perfection Servo consistently delivers exceptional repair services, rapid solutions, and prompt customer responses, with a focus on continuous improvement.
Each repair is backed by a 12-month operational warranty and meets the rigorous standards of ISO 9001:2015.
Quality Assurance
At Perfection Servo, we adapt our repair services to meet the specific needs of your operations by continuously enhancing our testing facilities to stay abreast of current industry standards. Our detailed testing process for industrial and automation repairs includes a 12-month warranty and features an exhaustive test report, which details the unit’s performance during our evaluations.
Additionally, we provide thorough reports with each repair, explaining the testing methods used and the results achieved. After evaluations, we issue clear, detailed quotes outlining the work needed to upgrade each unit to meet or exceed OEM standards. These detailed reports are essential for maintenance teams to effectively trace and address faults.
Credentials
Our Certified Repairs come with:
Expertly Trained and Certified Technicians – Our repair technicians are continuously educated to enhance their skills in both component repair and testing operations, with certifications from OEMs, the International Fluid Power Society, and the Electronics Technicians Association.
Rigorous System Testing – We subject each repair to intensive testing to ensure it conforms to or exceeds OEM specifications. Our tests simulate real-world operating conditions to assure the reliability of our repairs.
Premium Replacement Parts – We exclusively use new, OEM, or equivalent parts in our repairs. For rare or obsolete components, our engineers expertly craft suitable replacements.
Extensive Documentation – We diligently document every step of the repair process, from equipment manuals to detailed procedural steps. Each repair job is accompanied by a comprehensive report that outlines the actions taken and the testing conducted.
Repair Process
- Receiving: Upon arrival, parts are unpacked, cataloged, and photographed. We collect all necessary technical, order, and customer information to thoroughly prepare for the repair process. Each part is affixed with a tracking barcode for ongoing monitoring.
- Evaluation: Parts are forwarded to the appropriate department for a full evaluation.
- Quoting: Following the evaluation, our Inside Sales team drafts a detailed repair quote for your approval, detailing the restoration needed to achieve OEM standards and identifying any issues uncovered.
- Approval: After your approval, the repair is assigned to the technician best equipped for that specific part.
- Repair: The part undergoes specific repair and testing protocols. Our technicians replace any components showing signs of wear or potential failure, followed by an intensive testing phase.
- System/Quality Test: A Senior Technician reviews the part’s performance in our testing system post-testing, ensuring the Repair and Test Report is accurate and comprehensive.
- Test Reports: Each repaired unit is provided with a Test Report, which details its performance in the final testing. Most repairs also include an installation checklist, with our technicians ready to assist with installation and troubleshooting.
- Shipping: After repair completion, our automated system alerts the shipping department about any special shipping instructions from the customer. Each repair is carefully packaged to ensure it is protected during transit.