- Home
- Mechanical Repair
- Robot Wrist Assemblies
Robot Wrist Repair
Perfection Servo's Hydraulic/Mechanical division offers a superior option for repairing worn robot wrist assemblies, ensuring seamless operation of your robotic systems. Our experienced technicians specialize in servicing a wide range of robot wrists and assemblies, addressing issues such as wear, misalignment, and mechanical faults. Regular repair and maintenance of robot wrists are essential to prevent costly breakdowns and maintain optimal performance. By entrusting your robot wrist repair to Perfection Servo, you can extend the lifespan of your equipment and minimize downtime, ultimately enhancing productivity and efficiency in your operations.
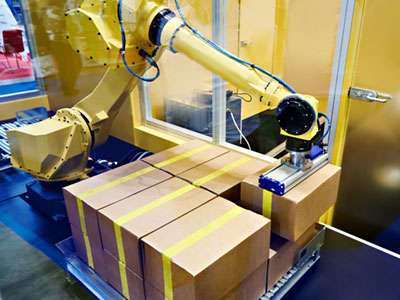
Common Robot Wrist Repair Needs
Robot wrist faults can result from various issues, including:
- Contamination
- Oil leaks
- Motor feedback
- Shorted motors
- Lack of Lubrications
- Unintended Collisions
Robot Wrist Repair Process
Perfection Servo is committed to providing exemplary repair services, efficient solutions, and quick turnarounds, continually focusing on improving our processes.
Each repair is guaranteed with a 12-month operational warranty and adheres to the ISO 9001:2015 quality standards.
Quality Assurance
Perfection Servo personalizes the repair experience to address your specific production needs by consistently enhancing our testing facilities to reflect the latest industry standards. Our rigorous testing protocol for industrial and automation repairs includes a 12-month warranty and features a detailed test report, which tracks the unit’s performance throughout the evaluation.
Additionally, our refined testing approach involves comprehensive reports for each repair, detailing the testing procedures and outcomes. We provide transparent and precise quotations after evaluations, specifying the refurbishment needed to elevate each unit to meet or surpass OEM standards. These reports are essential for maintenance teams to identify the root causes of breakdowns.
Credentials
Our Certified Repairs are recognized by:
Expertly Trained and Certified Technicians – Our repair technicians undergo continuous training to master both component repairs and testing system operations. Many of our technicians are certified by OEMs, the International Fluid Power Society, and the Electronics Technicians Association.
Rigorous System Testing – We perform detailed tests on each repair to ensure compliance with or surpass OEM specifications. Our testing environments simulate actual operational conditions to validate the reliability of our repairs.
Premium Replacement Parts – Only new, OEM, or equivalent parts are utilized in our repairs. For components that are proprietary or no longer in production, our engineers design and produce suitable replacements.
Extensive Documentation – Every phase of the repair process is documented thoroughly, from equipment manuals to specific procedural steps. Each repair is accompanied by a comprehensive report outlining the actions taken and the results from the testing.
Repair Process
- Receiving: When parts arrive, they are unpacked, cataloged, and photographed. We gather comprehensive technical, order-related, and customer information to fully prepare for the repair process. Each part is equipped with a tracking barcode for real-time monitoring.
- Evaluation: Each part is sent to the appropriate department for a detailed evaluation.
- Quoting: Following evaluation, our Inside Sales team compiles a detailed repair quote for approval, detailing the necessary actions to restore the unit to OEM standards, along with any identified problems.
- Approval: Upon receiving your approval, the repair is directed to the technician best equipped for that specific component.
- Repair: The part is treated with specified repair and testing procedures. Our technicians replace any components that are failing or at risk, followed by a detailed testing phase.
- System/Quality Test: After testing, a Senior Technician reviews the part’s function in our test setup and verifies the accuracy of the Repair and Test Report.
- Test Reports: Each repaired unit includes a Test Report that documents its performance in the final testing phase. Most repairs also come with an installation checklist, and our technicians are always available to assist with installation and troubleshooting.
- Shipping: Once repairs are complete, our automated system notifies the shipping department of any special shipping instructions from the customer. Each repair is securely packaged to ensure it is protected during transit.