- Home
- Mechanical Repair
- Spindles
Spindle Repair
At Perfection Servo, we have the specialized expertise and in-depth knowledge to repair and remanufacture all types of spindles and rotating devices in the manufacturing industry, from standard OEM offerings to custom-built products. Our ISO-certified spindle repair services help reduce operational downtime and lower the costs of future repairs and maintenance. Trust Perfection Servo to extend the life of your spindles and industrial operations.
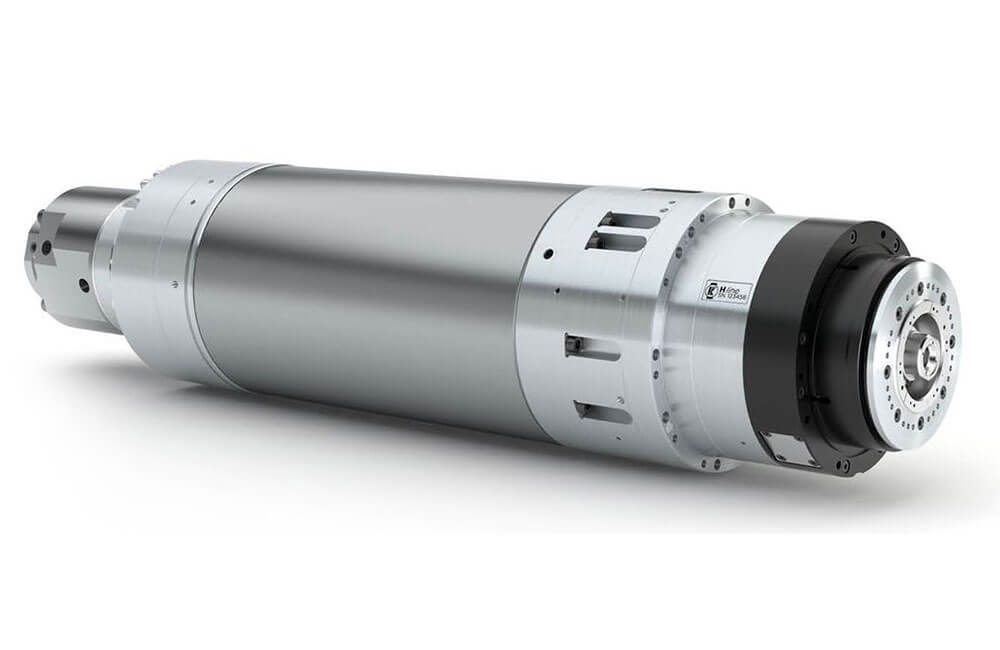
Signs Your Spindle Needs Repair
Common signs indicating that an industrial spindle may need repair include:
- Unusual Noises: High-pitched squeals, grinding, or knocking sounds during operation.
- Excessive Vibration: Abnormal or increased vibration, indicating potential bearing issues or imbalance.
- Decreased Precision: Inaccuracy in machining, leading to poor quality finishes or imprecise cuts.
- Overheating: The spindle becomes excessively hot during use, which can point to lubrication issues or bearing failure.
- Difficulty in Spindle Movement: Resistance or stiffness when the spindle starts or during operation, suggesting potential mechanical issues.
Spindle Repair Process
Perfection Servo is dedicated to providing top-notch repair services, timely solutions, and swift responses, constantly aiming to improve our offerings.
Each repair is backed by a 12-month operational warranty and meets the standards of ISO 9001:2015.
Quality Assurance
Perfection Servo tailors repair quality to fit your specific production requirements by continuously updating our testing facilities to stay aligned with the latest industry standards. Our in-depth industrial and automation repair testing is supported by a 12-month warranty and includes a comprehensive test report that documents the unit’s performance throughout our assessments.
We enhance our testing with detailed reports for each repair, which explain the procedures used and the results achieved. After evaluations, we issue transparent, detailed quotes that outline the necessary work to upgrade each unit to meet or exceed OEM standards. These reports are crucial for maintenance teams to trace the sources of failures.
Credentials
Our Certified Repairs are validated by:
Expertly Trained and Certified Technicians – Our technicians continuously receive training to ensure they are skilled in both component repair and the use of testing systems. Many technicians hold certifications from OEMs, the International Fluid Power Society, and the Electronics Technicians Association.
Rigorous System Testing – We rigorously test each repair to ensure it meets or exceeds OEM specifications. Our tests are conducted in environments that mimic actual operating conditions to ensure the accuracy of our repairs.
Premium Replacement Parts – We exclusively use new, OEM, or equivalent parts in our repairs. When dealing with proprietary or obsolete parts, our engineers carefully create suitable replacements.
Extensive Documentation – We thoroughly document every step of the repair process, from equipment manuals to detailed repair actions. Each job comes with a report that details the procedures followed and the tests conducted.
Repair Process
- Receiving: Upon arrival, parts are unpacked, cataloged, and photographed. We collect all relevant technical, order-related, and customer details to fully understand the repair needs. Each part is assigned a tracking barcode to ensure tracking throughout the repair process.
- Evaluation: Parts are forwarded to the appropriate department for a comprehensive evaluation.
- Quoting: After evaluation, our Inside Sales team drafts a precise repair quote for your approval, detailing the restoration needed to achieve OEM standards and noting any issues found.
- Approval: With your consent, the repair is assigned to the technician best suited for that specific part.
- Repair: The part undergoes designated repair and testing protocols. Our technicians replace all components that are failing or are likely to fail, followed by a thorough testing stage.
- System/Quality Test: Following the tests, a Senior Technician assesses the part’s performance within our testing systems and validates the Repair and Test Report.
- Test Reports: Each repaired unit comes with a Test Report detailing its performance during the final testing phase. Most repairs also include an installation checklist, and our technicians stand ready to assist with installation and troubleshooting.
- Shipping: After repairs are finalized, our automated system alerts the shipping department about any specific customer shipping preferences. Each repair is securely packaged to ensure it arrives undamaged.