- Home
- Hydraulic Repair
- Pumps
Hydraulic Pump Repair
Perfection Servo excels in repairing a variety of hydraulic pumps, including gear pumps, piston pumps, smart pumps, vacuum pumps, and vane pumps, adhering to OEM standards. Our skilled technicians, trained by various OEMs, bring extensive experience to every step of the repair process. Each pump undergoes meticulous remanufacturing and rigorous testing to ensure optimal function under load. With precision-machined internals and reliance on quality hydraulic fluid, we address common issues such as leaks and loss of efficiency. Our OEM-certified facility conducts final testing in simulated real-world conditions, ensuring compliance with specifications before completion. Trust Perfection Servo for comprehensive and reliable hydraulic pump repairs.
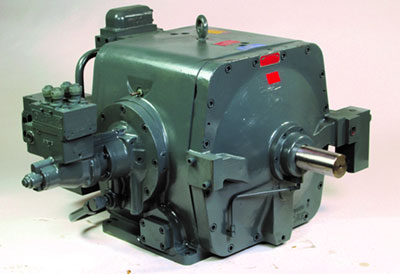
Hydraulic Pump Repair Process
Our commitment to providing customers with exceptional repair quality, effective problem-solving, and swift service is upheld through ongoing improvements in quality.
Every Certified Repair is supported by a 12-month operational warranty from Perfection Servo. ISO 9001: 2015 Certified.
Quality Assurance
To align the quality of repairs with the specific needs of your production environment, Perfection Servo routinely updates and maintains our testing equipment to adhere to the highest industry standards. In our comprehensive industrial and automation repair testing, we ensure a 12-month in-service warranty for our clients. Each repair from Perfection Servo includes a test report, showcasing how the unit performed in our tests.
Additionally, our advanced testing processes are complemented by detailed reports for each repair, showing the testing methods and outcomes. For repairs that are assessed, we offer precise quotes detailing the necessary steps to refurbish the unit to meet or surpass OEM standards. These reports aid your maintenance teams in pinpointing the primary cause of failures.
Credentials
Perfection Servo's repairs are accredited as follows:
- Factory Trained and Certified Technicians – Our repair technicians are continuously trained and familiarized with their respective fields. They are not only proficient in repairing the components but also skilled in using the testing systems. Many have received training or certification from OEMs, the International Fluid Power Society, and the Electronics Technicians Association.
- System Testing – Every repair is subject to rigorous testing, ensuring it meets or exceeds OEM specifications. Our tests simulate plant environment conditions to confirm the accuracy of repairs.
- Quality Replacement Parts – We exclusively use new OEM or equivalent parts. In cases of proprietary or outdated equipment, our engineers design suitable replacement parts.
- Detailed Documentation – We document every aspect of our process, from equipment manuals to precise repair procedures. Each repair includes a comprehensive report detailing the work done and the testing procedures.
Repair Process
- Receiving: All received parts are unpacked, logged, and photographed. Our system meticulously records all technical, order-related, and customer-specific information to fully understand the repair scope. Each part is assigned a tracking barcode for monitoring throughout the repair process.
- Evaluation: Received parts are sent to the relevant department for thorough evaluation.
- Quoting: After evaluation, our Inside Sales team reaches out with a detailed repair quotation for review and approval. The quotation includes what is needed to restore the unit to OEM specifications and the issues found, aiding in identifying failure causes.
- Approval: With your approval, the repair is added to the workflow of the technician best suited for that specific part.
- Repair: Our system aligns your part with the appropriate repair and test procedures, ensuring a thorough and accurate restoration. Technicians replace all components that have failed or are likely to fail, followed by extensive testing.
- System/Quality Test: Post-testing, a Senior Technician reviews the part's performance in its test system and assesses the Repair and Test Report for thoroughness and accuracy.
- Test Reports: Each repaired unit is shipped with a Test Report detailing how it fared in the final test. Often, this is accompanied by an installation checklist. Our technicians are always available to assist with installation and troubleshooting.
- Shipping: Upon repair completion, our system notifies the shipping department of any specific customer requirements. Repairs are packaged securely to ensure they arrive without any shipping damage.