- Home
- Hydraulic Repair
- Hydraulic Motors
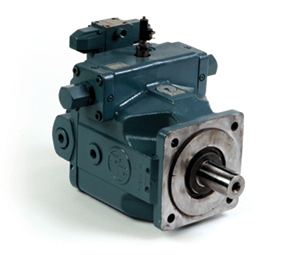
Hydraulic Motor Repair
At Perfection Servo, we excel in repairing gear motors, piston motors, rotary actuators, and vane motors, recognizing their vital role in industrial operations. Our prompt turnaround and emergency service options ensure minimal downtime, with repairs completed within 24 to 72 hours. Rest assured, our specialized testing equipment ensures compliance with OEM standards. Regular maintenance and timely repairs of gear motors, piston motors, rotary actuators, and vane motors are essential for sustaining operational efficiency and prolonging equipment lifespan. Trust Perfection Servo for expert repair solutions that keep your motors functioning at their best.
Motor Repair Process
We are dedicated to providing our clients with superior repair work, practical solutions, and prompt services, constantly striving for quality enhancements.
Every Certified Repair comes with Perfection Servo's 12-month operational warranty. ISO 9001: 2015 Accredited.
Quality Assurance
Perfection Servo ensures the repair quality meets your unique production needs by frequently updating our testing facilities to conform to the latest industry benchmarks. Our exhaustive testing process in industrial and automation repair includes a 12-month warranty for our clients, and we provide a comprehensive test report with each Perfection Servo repair, illustrating the unit’s performance during tests.
In addition, our sophisticated testing routines are supplemented with detailed reports for each repair, outlining the testing protocols and results. When repairs are evaluated, we offer clear quotations, listing the requirements for refurbishing the unit to either meet or exceed OEM standards. These informative reports are instrumental for maintenance teams in identifying failure causes.
Credentials
Our Certified Repairs are endorsed by the following credentials:
Expertly Trained and Certified Technicians – Our repair technicians undergo continuous training in their respective fields, ensuring proficiency not just in repairing components but also in utilizing testing systems. Many hold certifications from OEMs, the International Fluid Power Society, and the Electronics Technicians Association.
Rigorous System Testing – We test each repair thoroughly, aiming to match or exceed OEM specifications. Our testing environment simulates actual plant conditions to guarantee repair accuracy.
Premium Replacement Parts – Only new OEM or equivalent parts are used in our repairs. When dealing with proprietary or outdated equipment, our engineers craft appropriate replacements.
Extensive Documentation – We meticulously document every step, from equipment manuals to detailed repair procedures. A repair report accompanies each job, outlining the actions taken and the testing processes.
Repair Process
- Receiving: Upon arrival, parts are unpacked, cataloged, and photographed. Our system collects all necessary technical, order-related, and customer information to ensure a comprehensive understanding of the repair requirements. We then attach a tracking barcode to each part for monitoring throughout the repair process.
- Evaluation: Each part is directed to the relevant department for a thorough assessment.
- Quoting: Following assessment, our Inside Sales team provides a detailed repair quote for your approval, including what needs to be done to restore the unit to OEM standards and detailing any identified problems.
- Approval: Once we receive your approval, the repair is assigned to the technician best equipped to handle that type of part.
- Repair: Your part is matched with the appropriate repair and test procedures. Our Technicians replace all failing and potentially faulty components, followed by a comprehensive testing phase.
- System/Quality Test: After testing, a Senior Technician evaluates the part’s operation in the test system and verifies the accuracy of the Repair and Test Report.
- Test Reports: Each repaired unit includes a Test Report outlining its performance in the final test. Additionally, most repairs come with an installation checklist. Our technicians are always ready to offer assistance with installation and troubleshooting.
- Shipping: After repair completion, our automated system informs the shipping department of any special customer shipping requirements. Repairs are securely packaged to prevent damage during transit.