- Home
- Hydraulic Repair
- Valves
Valve Repair
Perfection Servo, with its ISO certification, specializes in valve repair services, recognizing the critical role valves play in industrial operations. Whether it's directional valves, proportional valves, or servo valves, these components are integral to the smooth functioning of machinery and processes. Regular maintenance and timely repair of valves are paramount to ensuring uninterrupted production, minimizing downtime, and optimizing efficiency. With our expertise and commitment to excellence, we offer cost-effective repair solutions tailored to various industrial applications, helping businesses maintain operational continuity and maximize productivity.
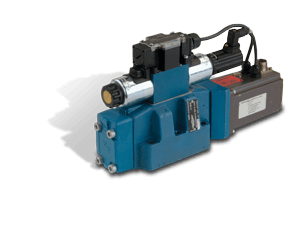
Valve Repair Process
At Perfection Servo, we are committed to providing outstanding valve repair services, innovative solutions, and quick response times, with a continuous aim to enhance quality.
Each Certified Repair is backed by a 12-month operational guarantee under Perfection Servo and adheres to the ISO 9001:2015 standards.
Quality Assurance
Perfection Servo adapts repair quality to precisely fit your production needs by regularly modernizing our testing facilities to reflect the latest industry criteria. Our extensive testing regimen for industrial and automation repairs comes with a 12-month warranty and includes a detailed test report for each repair, documenting the unit’s operational performance during testing.
Moreover, our refined testing procedures include comprehensive reports for each repair, detailing the methodologies used and the results achieved. Clear and detailed quotations are provided after assessments, describing the necessary refurbishments to elevate the unit to or beyond OEM specifications. These detailed reports are essential for maintenance teams to determine failure origins.
Credentials
Our Certified Repairs are bolstered by:
Expertly Trained and Certified Technicians – Our repair technicians continually undergo training to excel in component repair and testing system operations, with many holding certifications from OEMs, the International Fluid Power Society, and the Electronics Technicians Association.
Rigorous System Testing – Every repair is extensively tested to ensure it matches or surpasses OEM standards. Our test settings replicate real-world plant conditions to verify the precision of repairs.
Premium Replacement Parts – Only new, OEM, or equivalent parts are used in our repairs. For proprietary or outdated equipment, our engineers meticulously create appropriate replacements.
Extensive Documentation – We comprehensively document each stage of the repair process, from equipment manuals to detailed repair actions. Every job is accompanied by a repair report that outlines the steps performed and the tests conducted.
Repair Process
- Receiving: Upon receipt, parts are unpacked, cataloged, and photographed. We collect all relevant technical, order-related, and customer data to fully grasp the repair requirements. Each part is then marked with a tracking barcode for progress monitoring throughout the repair process.
- Evaluation: Parts are dispatched to the appropriate department for detailed evaluation.
- Quoting: Post-evaluation, our Inside Sales team issues a precise repair quote for your approval, specifying the necessary restoration work to meet OEM standards and highlighting any detected problems.
- Approval: After receiving your go-ahead, the repair is assigned to the technician best suited for the specific part.
- Repair: The part is processed according to tailored repair and testing protocols. Our technicians replace any defective or suspect components, followed by a thorough testing phase.
- System/Quality Test: Following testing, a Senior Technician reviews the part's function in our testing systems and confirms the accuracy of the Repair and Test Report.
- Test Reports: Each repaired unit includes a Test Report detailing its efficacy in the final test. Most repairs also come with an installation checklist, and our technicians are available for installation support and troubleshooting.
- Shipping: Once repairs are finalized, our automated system alerts the shipping department about any special shipping instructions from the customer. Repairs are carefully packaged to ensure they are protected during transit.