- Home
- Mechanical Repair
- Ballscrews
Ballscrew Repair
Perfection Servo provides comprehensive ballscrew repair and restoration services in our ISO-Certified facilities. We specialize in precise repairs across various types of ballscrews, including Acme, Rolled Thread, and Precision Ground assemblies from multiple manufacturers. With extensive experience across different brands and types, we swiftly evaluate and restore ballscrews to optimal condition, offering potential savings of up to 50% compared to replacement costs.
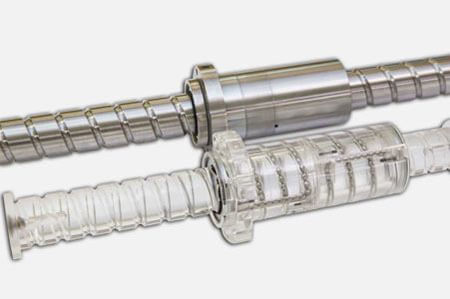
Do You Need Ballscrew Repair?
Common indicators of ballscrew issues include:
- Pitted exterior
- Signs of corrosion
- Heat discoloration
- Unusual sounds like wobbling, chattering, or growling (often suggesting alignment issues) lubrication needs
- General deterioration
Ballscrew Repair Process
Perfection Servo is committed to delivering exceptional repair services, cutting-edge solutions, and rapid responses, continuously striving for better results.
Each repair is supported by a 12-month operational warranty and conforms to ISO 9001:2015 standards.
Quality Assurance
Perfection Servo customizes repair quality to meet your specific production needs by constantly upgrading our testing facilities to keep pace with the most recent industry standards. Our comprehensive testing for industrial and automation repairs includes a 12-month warranty and comes with a detailed test report, capturing the unit’s performance during our evaluations.
We also provide thorough reports for each repair, detailing the testing procedures used and the results obtained. Clear, detailed quotes are issued after evaluations, specifying the necessary refurbishments to bring each unit up to or beyond OEM standards. These reports are vital for maintenance teams to understand the reasons behind failures.
Credentials
Our Certified Repairs are supported by:
Expertly Trained and Certified Technicians – Our technicians are continually trained to be proficient in both component repair and the operation of testing systems. Many have certifications from OEMs, the International Fluid Power Society, and the Electronics Technicians Association.
Rigorous System Testing – We conduct thorough tests on each repair to ensure they meet or exceed OEM specifications. Our testing environments simulate actual operational conditions to confirm the precision of the repairs.
Premium Replacement Parts – We use only new, OEM or equivalent parts in our repairs. For outdated or proprietary components, our engineers design appropriate replacements.
Extensive Documentation – We document each step of the repair process in detail, from equipment manuals to specific repair procedures. Each job is accompanied by a report that outlines the actions taken and the tests conducted.
Repair Process
- Receiving: When parts arrive, they are unpacked, cataloged, and photographed. We gather all necessary technical, order-related, and customer information to thoroughly understand the repair requirements. Each part is marked with a tracking barcode for follow-up throughout the repair process.
- Evaluation: Each part is sent to the relevant department for an in-depth evaluation.
- Quoting: Following evaluation, our Inside Sales team provides a detailed repair quote for your approval, outlining what needs to be done to bring the unit up to OEM standards and any identified issues.
- Approval: Once we receive your approval, the repair is assigned to the technician best equipped for that type of part.
- Repair: The part is processed using designated repair and testing procedures. Our technicians replace any defective or potentially problematic components, followed by an extensive testing phase.
- System/Quality Test: After the testing phase, a Senior Technician reviews the part’s performance in the test system and confirms the accuracy of the Repair and Test Report.
- Test Reports: Each repaired unit includes a Test Report that details its performance in the final tests. Most repairs also come with an installation checklist, and our technicians are available to help with installation and troubleshooting.
- Shipping: Once the repair is complete, our automated system informs the shipping department of any special customer shipping requirements. Repairs are carefully packaged to prevent any damage during transit.