- Home
- Electronic Repair
- Drives
Drive Repair
Perfection Servo's specialization in drive repair spans over 35 years, encompassing a wide array of drives including AC Inverters, DC Inverters, Servo Drives, Spindle Drives, Stepper Drives, and VFDs (Variable Frequency Drives). Our ISO-Certified Industrial Repair Process commences with a thorough evaluation to detect both evident and potential defects, ensuring comprehensive restoration. With the support of over 500 specialized test stands, our expert technicians rigorously test each repair to meet stringent quality standards, accompanied by detailed reports and operational warranties. We recognize the critical importance of drive repair in maintaining smooth industrial operations, and our dedication to excellence ensures minimal downtime and optimized performance for your systems.
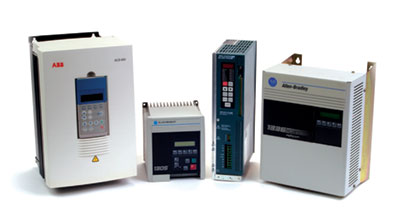
Does My Drive Need Repair?
In addition to obvious physical damage or performance issues, signs that your drive may need repair include:
- Unusual noises such as grinding or screeching
- Unresolvable error codes or alarms on diagnostic systems
- Reduced movement speed and accuracy
- Overheating that is not related to environmental factors
- Excessive vibration
- Failure to respond to commands or incorrect data transmission
- Inconsistencies in power supply
Drive Repair Process
At Perfection Servo, we offer expert industrial repair services, innovative solutions, and efficient response times. Every repair comes with a 12-month operational warranty and meets ISO 9001:2015 standards.
Quality Assurance
Perfection Servo customizes repair quality to align with your specific production requirements by continuously updating our testing facilities to the latest industry standards. Our in-depth testing for industrial and automation repairs includes a 12-month warranty and is accompanied by a comprehensive test report, which details the unit’s performance throughout our evaluation.
We further refine our testing with detailed reports for each repair, outlining the methodologies employed and the outcomes achieved. Transparent, comprehensive quotes are provided after evaluations, detailing the refurbishment required to elevate each unit to or above OEM standards. These reports are invaluable for maintenance teams to trace the origins of malfunctions.
Credentials
Our Certified Repairs are backed by:
Expertly Trained and Certified Technicians – Our repair technicians receive ongoing training, excelling in both component repair and testing system operations. Many hold certifications from OEMs, the International Fluid Power Society, and the Electronics Technicians Association.
Rigorous System Testing – Each repair undergoes exhaustive testing to ensure it conforms to or exceeds OEM specifications. Our testing environments mimic real-world plant conditions to ensure repair accuracy.
Premium Replacement Parts – We exclusively use new, OEM, or equivalent parts in our repairs. For proprietary or obsolete components, our engineers create suitable replacements.
Extensive Documentation – Every step of the repair process is documented in detail, from equipment manuals to the specific repair procedures undertaken. Each repair job includes a report that outlines the actions taken and the testing conducted.
Repair Process
- Receiving: Upon receipt, parts are unpacked, cataloged, and photographed. We collect essential technical, order-related, and customer data to thoroughly understand the repair requirements. Each part is labeled with a tracking barcode for monitoring throughout the repair process.
- Evaluation: Directed to the relevant department, each part undergoes a detailed evaluation.
- Quoting: After evaluation, our Inside Sales team generates a precise repair quote for your approval, listing necessary restorative actions to meet OEM standards and any issues identified.
- Approval: Following your approval, the repair is allocated to the technician best suited to handle that particular part.
- Repair: The part is treated according to specific repair and testing protocols. Our technicians replace any faulty or suspect components, followed by a rigorous testing phase.
- System/Quality Test: Once tested, a Senior Technician assesses the part’s function within our test system and confirms the accuracy of the Repair and Test Report.
- Test Reports: Each repaired unit comes with a Test Report showcasing its performance during the final testing. Most repairs also include an installation checklist, with our technicians ready to assist with installation and troubleshooting.
- Shipping: After repairs are completed, our automated system notifies the shipping department of any special shipping instructions from the customer. Repairs are securely packaged to prevent damage during transit.