- Home
- Electronic Repair
- HMI's
HMI Repair Service
At Perfection Servo, we specialize in intricate industrial human-machine interface (HMI) repairs, vital for modern automation. Our team adeptly restores Allen Bradley, Fanuc and Siemens HMIs, addressing various issues such as touchscreen damage, power supply failures, LCD screen issues, battery failure, contamination, bezel and housing damage, and display problems. From repairing wear and damage to resolving program loss issues, our comprehensive expertise ensures HMIs regain full functionality, enhancing operational efficiency in industrial settings.
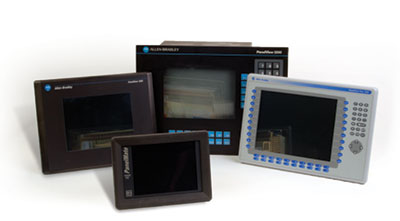
Does My HMI Need Repair?
If you have any of the following issues with your HMI equipment, Perfection Servo can help:
- Touchscreen Issues: Unresponsiveness, calibration problems, or physical damage to the touchscreen.
- Display Problems: Dimming, flickering, dead pixels, or complete loss of display.
- Communication Failures: Difficulty in interfacing with other control systems, or signal transmission issues.
- Power Issues: Inconsistent power supply, failure to power up, or electrical shorts.
- Software or Configuration Errors: Glitches, freezing, or issues with the HMI software, including corrupted data or configuration problems.
HMI Repair Process
Perfection Servo is focused on delivering exceptional repair services, innovative solutions, and rapid responses, continually striving to enhance our processes.
Each repair we perform is covered by a 12-month operational warranty and is compliant with ISO 9001:2015 standards.
Quality Assurance
Perfection Servo customizes repair services to fit your specific operational demands by regularly upgrading our testing facilities to incorporate the latest industry standards. Our detailed testing protocol for industrial and automation repairs is supported by a 12-month warranty and includes a comprehensive report documenting the unit’s performance throughout the assessment period.
Furthermore, our enhanced testing framework produces detailed reports for every repair, outlining the techniques used and the results obtained. Clear, precise quotes are issued following these evaluations, describing the required work to enhance each unit to meet or exceed OEM standards. These reports are vital for maintenance teams to pinpoint the sources of faults.
Credentials
Our Certified Repairs are validated by:
Expertly Trained and Certified Technicians – Our technicians are regularly trained to maintain expertise in component repair and testing operations, holding certifications from OEMs, the International Fluid Power Society, and the Electronics Technicians Association.
Rigorous System Testing – Each repair is subjected to intensive testing to ensure it aligns with or surpasses OEM specifications. We conduct these tests under conditions that mimic actual operational environments, guaranteeing the accuracy of our repairs.
Premium Replacement Parts – We use only new, OEM, or equivalent quality parts in all repairs. For parts that are proprietary or discontinued, our engineers competently fabricate appropriate replacements.
Extensive Documentation – We meticulously document each step of the repair process, from the initial equipment manuals to the detailed repair procedures. Each job is accompanied by a comprehensive report detailing the steps taken and the testing outcomes.
Repair Process
- Receiving: Upon arrival, parts are unpacked, cataloged, and photographed. We compile essential technical, order-related, and customer-specific details to fully understand the repair scope. Each part is then marked with a tracking barcode for efficient progress tracking.
- Evaluation: Each part is sent to the relevant department for a thorough evaluation.
- Quoting: After evaluation, our Inside Sales team prepares a detailed repair quote for your approval, outlining the necessary work to restore the unit to OEM standards and highlighting any issues found.
- Approval: Once approved, the repair is assigned to the technician best suited for the specific component.
- Repair: The part is processed according to tailored repair and testing protocols. Our technicians replace any worn or potentially faulty components, followed by a comprehensive testing phase.
- System/Quality Test: After testing, a Senior Technician reviews the part’s function in our test system and verifies the completeness and accuracy of the Repair and Test Report.
- Test Reports: Each repaired unit includes a Test Report detailing its performance during the final testing. Most repairs also include an installation checklist, and our technicians are available to assist with installation and troubleshooting.
- Shipping: Once the repairs are complete, our automated system notifies the shipping department of any special customer shipping requirements. Each repair is securely packaged to ensure it arrives in pristine condition.