- Home
- Hydraulic Repair
- Cylinders
Hydraulic Cylinder Repair
Count on Perfection Servo for crucial hydraulic cylinder repairs, integral to the efficiency of your operations. Malfunctioning cylinders can result in significant downtime and costly disruptions. Our dedicated team specializes in hydraulic cylinder repair, delivering top-notch, dependable solutions tailored to your needs. We expertly handle a wide range of cylinder types, including mill duty cylinders and precision actuators, We offer repairs for single and double-ended configurations, as well as components like rods, seals, piston heads, gland nuts, and tubes of all sizes. Regular maintenance and timely repairs of hydraulic cylinders, mill duty cylinders, and precision actuators are essential for sustaining operational efficiency and minimizing downtime. Trust Perfection Servo for expert repair services that keep your operations running smoothly.
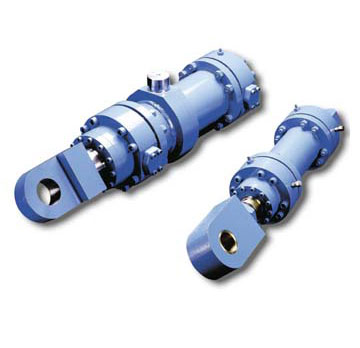
Cylinder Repair Process
We ensure each cylinder is disassembled, cleaned, and inspected thoroughly. Dynamic testing after repair confirms optimal performance and leak-free operation. Our pressure testing reaches up to 3,000 psi, and we use replacement seals rated for up to 6,000 psi and 500°F.
For hydraulic cylinder repairs that extend your products’ lifespan and enhance your operational efficiency, trust Perfection Servo.
Perfection Servo is committed to providing our clients with outstanding repair services, effective solutions, and swift response times, always aiming for continuous improvement.
Each Certified Repair includes a 12-month operational warranty under Perfection Servo and is certified under ISO 9001:2015.
Quality Assurance
To ensure that our repair quality meets your specific production requirements, Perfection Servo regularly updates our testing facilities to meet the latest industry standards. Our comprehensive testing process for industrial and automation repairs is backed by a 12-month warranty, and we include a detailed test report with each repair, showing the unit’s performance during testing.
Additionally, our advanced testing methods come with in-depth reports for each repair, specifying the tests conducted and the results obtained. We provide detailed quotes upon evaluation, explaining the necessary steps to refurbish the unit to meet or exceed OEM standards. These reports are vital for maintenance teams to identify the causes of failures.
Credentials
Our Certified Repairs are supported by:
Expertly Trained and Certified Technicians – Our technicians receive ongoing training and are skilled in both component repair and testing system usage. Many possess certifications from OEMs, the International Fluid Power Society, and the Electronics Technicians Association.
Rigorous System Testing – We conduct extensive testing on each repair to ensure it meets or exceeds OEM specifications. Our testing environments replicate actual plant conditions to ensure the accuracy of the repairs.
Premium Replacement Parts – We use only new, OEM or equivalent parts in our repairs. When dealing with proprietary or obsolete equipment, our engineers develop suitable replacements.
Extensive Documentation – Every step of the repair process is thoroughly documented, from equipment manuals to detailed repair procedures. Each job comes with a repair report outlining the actions taken and the testing conducted.
Repair Process
- Receiving: Upon receiving, parts are unpacked, cataloged, and photographed. We gather all necessary technical, order-related, and customer information to fully understand the repair needs. Each part is then tagged with a tracking barcode to facilitate monitoring throughout the repair process.
- Evaluation: Each part is routed to the appropriate department for a thorough assessment.
- Quoting: Following the assessment, our Inside Sales team provides a detailed repair quote for your approval, listing the necessary actions to restore the unit to OEM standards and noting any identified issues.
- Approval: Upon your approval, the repair is allocated to the technician best equipped for that specific part.
- Repair: The part is aligned with the appropriate repair and test procedures. Our technicians replace any failing or potentially faulty components and then proceed to an exhaustive testing phase.
- System/Quality Test: After testing, a Senior Technician reviews the part’s operation within the test system and verifies the accuracy of the Repair and Test Report.
- Test Reports: Each repaired unit is provided with a Test Report detailing its performance in the final tests. Most repairs also include an installation checklist, and our technicians are always ready to assist with installation and troubleshooting.
- Shipping: After the repair is complete, our automated system notifies the shipping department of any special customer shipping instructions. Repairs are securely packaged to prevent damage during transit.