- Home
- Electronic Repair
- Welders
Welder Repair
At the forefront of the industry, Perfection Servo stands as the premier provider of welding machine repair services. Our dedicated team excels in the intricate art of welder repair, addressing a wide array of weld controls with precision and expertise. We prioritize the longevity and reliability of your equipment by subjecting every repair to meticulous dynamic testing under load, guaranteeing both optimal functionality and long-lasting durability.
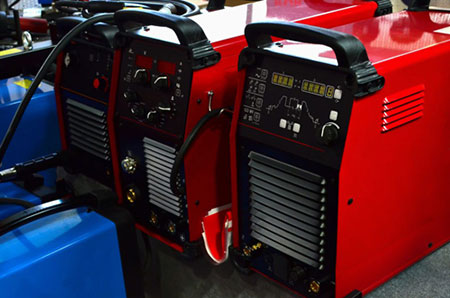
Signs Your Welder Needs Repair
In addition to any apparent physical damage, signs that a welder needs repair include:
- Inconsistent welding results, like uneven welds or variation in penetration
- Excessive spatter during welding operations
- Unusual noises or vibrations when the welder is in use
- Difficulty in starting or maintaining an arc
- Overheating of the welder during use
Welder Repair Process
Perfection Servo is dedicated to providing premium repair services, responsive solutions, and reliable customer support, with a continual focus on enhancing our operations.
Each repair is backed by a 12-month operational warranty and strictly adheres to ISO 9001:2015 standards.
Quality Assurance
Perfection Servo customizes our repair processes to meet the specific demands of your operations by keeping our testing facilities updated with the most recent industry standards. Our thorough testing protocol for industrial and automation repairs includes a 12-month warranty and a detailed test report that reviews the unit’s performance during our evaluations.
Additionally, we issue comprehensive reports for each repair, detailing the testing procedures and outcomes. Following the evaluation, we provide clear and precise quotations that outline the necessary adjustments to elevate each unit to meet or exceed OEM standards. These reports are critical for maintenance teams to efficiently diagnose and resolve issues.
Credentials
Our Certified Repairs are supported by:
Expertly Trained and Certified Technicians – Our technicians continuously update their skills through training, excelling in both component repair and testing procedures. They hold certifications from reputable OEMs, the International Fluid Power Society, and the Electronics Technicians Association.
Rigorous System Testing – We conduct detailed tests on each repair to ensure compliance with or exceed OEM specifications. Our testing conditions replicate actual operational environments to verify the reliability of our repairs.
Premium Replacement Parts – We only use new, OEM, or equivalent quality parts in our repairs. For components that are rare or no longer in production, our engineers skillfully fabricate appropriate replacements.
Extensive Documentation – Every stage of the repair process is thoroughly documented, from the initial equipment manuals to the specific steps taken during repairs. Each repair includes a detailed report that outlines the procedures performed and the outcomes of the tests.
Repair Process
- Receiving: Upon their arrival, parts are unpacked, cataloged, and photographed. We compile all necessary technical, order-related, and customer information to fully prepare for the repair process. Each part is marked with a tracking barcode for effective oversight.
- Evaluation: Parts are routed to the appropriate department for a comprehensive evaluation.
- Quoting: After evaluation, our Inside Sales team generates a detailed repair quote for your approval, detailing the necessary actions to restore the unit to OEM standards and identifying any issues found.
- Approval: Once you approve, the repair is allocated to the technician best suited for that specific component.
- Repair: The part undergoes tailored repair and testing protocols. Our technicians replace any components that are worn or potentially defective, followed by a thorough testing phase.
- System/Quality Test: Following the testing phase, a Senior Technician reviews the part’s functionality within our test system and verifies the completeness and accuracy of the Repair and Test Report.
- Test Reports: Each repaired unit is provided with a Test Report that details its performance in the final tests. Most repairs also include an installation checklist, and our technicians are ready to provide assistance with installation and troubleshooting.
- Shipping: After completion, our automated system notifies the shipping department of any specific shipping instructions from the customer. Each repair is carefully packaged to ensure it is delivered in perfect condition.