- Home
- Electronic Repair
- Servo Motors
Motor Repair
Perfection Servo is your trusted partner for swift emergency repairs, with turnaround times ranging from 24 to 72 hours, covering a comprehensive range of electric motors including servo, AC, and DC motors, as well as spindle and stepper motors. Our state-of-the-art testing facilities, which include a specialized fractional HP Servo Motor Load Stand, allow us to expertly install, align, and dynamically load test motors, ensuring they meet and exceed OEM specifications.
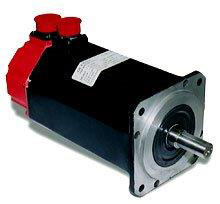
Does My Electric Motor Need Repair?
Apart from physical damage, there are several indicators that an industrial electric motor might require repair:
- Excessive Heat: Overheating during operation, which could be a sign of overload or internal friction.
- Vibration or Unusual Noises: Increased vibration or strange noises like grinding or humming during operation.
- Reduced Performance: Noticeable decrease in speed, torque, or overall efficiency.
- Erratic Behavior: The motor starts and stops unpredictably or changes speeds erratically.
- Electrical Issues: Frequent tripping of circuit breakers or blown fuses when the motor is in use, which can indicate electrical problems.
Electronic Repair Process
We focus on delivering exceptional repair services, finding effective solutions, and ensuring rapid service, all while continually elevating our quality standards.
Perfection Servo’s 12-month operational warranty backs every Certified Repair.
Adherence to ISO 9001: 2015 Standards
Quality Assurance
At Perfection Servo, we align repair quality with your production requirements, consistently upgrading our testing facilities to reflect the latest industry standards. Our industrial and automation repair testing process comes with a 12-month warranty for clients, and each repair is accompanied by an exhaustive test report, indicating the unit's performance during our rigorous testing.
Furthermore, our cutting-edge testing methods include detailed reports for each repair, detailing the tests conducted and the results obtained. For repairs requiring evaluation, we provide transparent quotes, explaining the steps necessary to refurbish the unit to meet or exceed OEM standards. These comprehensive reports aid maintenance teams in identifying and addressing the underlying reasons for malfunctions.
Credentials
The credentials for our Certified Repairs include:
- Highly Skilled and Certified Technicians – Our technicians are continually educated in their areas of expertise, ensuring skillfulness in component repairs and system testing. Many hold certifications from OEMs, the International Fluid Power Society, and the Electronics Technicians Association.
- Comprehensive System Testing – All repairs undergo thorough testing to surpass or match OEM specifications. Our testing replicates the conditions of a plant environment to guarantee the fidelity of the repairs.
- Superior Replacement Parts – In our repairs, we use only new, OEM, or equivalent parts. Our engineering team crafts replacements for unique or outdated components.
- Detailed Documentation – Every step of our process, from equipment manuals to intricate repair procedures, is fully documented. A detailed report accompanies each repair, outlining the procedures followed and the testing conducted.
Repair Process
- Receiving: Every part received is meticulously unpacked, recorded, and photographed. Our system captures all critical technical, order-specific, and client information to grasp the full extent of the repair. Each part is marked with a tracking barcode, enabling its progress through the repair process to be monitored.
- Evaluation: Parts are forwarded to the appropriate department for comprehensive evaluation.
- Quoting: Post-evaluation, our Inside Sales team provides an itemized repair quote for your approval, detailing what is required to bring the unit back to OEM conditions and highlighting the issues found.
- Approval: Upon receiving your go-ahead, the repair is allocated to the technician most qualified for that particular part.
- Repair: Linked to the correct repair and test protocols, our technicians diligently replace both failed and at-risk components. Subsequent testing ensures the repair’s thoroughness.
- System/Quality Test: Following the testing phase, a Senior Technician reviews the part’s performance and the completeness of the Repair and Test Report.
- Test Reports: Each repaired unit is sent with a Test Report outlining its performance during the final testing phase. Most repairs also come with an installation checklist, and our technicians are readily available for installation guidance and troubleshooting.
- Shipping: Once repairs are complete, our automated system informs the shipping department of any unique shipping requirements. All repairs are securely packed to prevent any damage during transport.